The ENEOS Group’s Innovative Technologies and Open Innovation
- Renewable energy
- Hydrogen
- MCH
- Biomass
- Bioethanol
- Recycle
- Circular economy
- Materials
- Preferred Networks
- AI
- Matlantis
- Organic-type catalysts
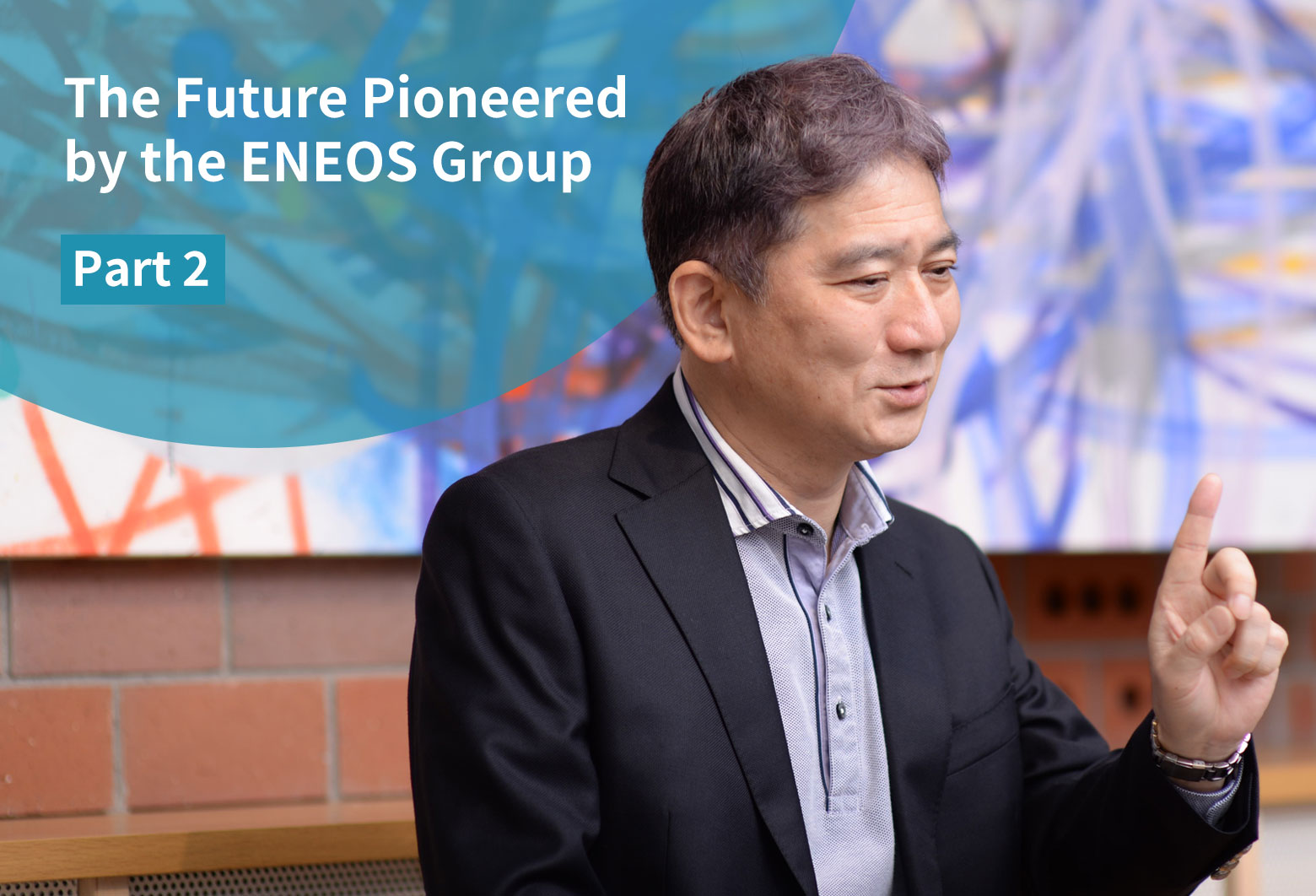
The ENEOS Group, as a leader in the energy and materials industry, aims to achieve a carbon-neutral society by 2050 while utilizing renewable energy, biomass, and carbon dioxide capture and storage (CCS). In this three-part series, we asked Fujiyama Yuichiro, CTO of ENEOS Holdings, what kind of technological development and strategies the Group is pursuing to achieve this goal. In the previous article (Part 1), we asked about the three main parts of the ENEOS Group's technological development: renewable energy, biomass, and CCS. In addition, the technology using hydrogen to match energy supply and demand for the efficient use of renewable energy was described. In the Part 2, we will delve into the various innovative technologies being developed by the ENEOS Group.
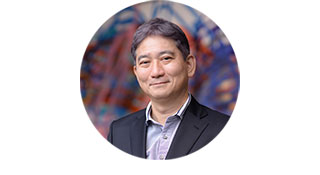
Senior Vice President, CTO
ENEOS Holdings, Inc.
MCH and synthetic fuels are gaining attention in the field of renewable energy.
Matlantis™, a simulator developed through a collaborative project with Preferred Networks, has brought innovation to the development of materials.
—Can you tell us more about technological development in the ENEOS Group?
Fujiyama: The amount of electricity generated from renewable energy, such as solar and wind power, depends on weather conditions and wind levels on any given day. Energy storage technology is required to ensure a stable supply, which is where hydrogen is coming into the spotlight. Electricity generated from renewable energy can be stored and transported much more easily when transformed into hydrogen by water electrolysis.
There’re several known methods of storing and transporting hydrogen. Among them, the method of converting hydrogen into a liquid with gasoline-like properties called methylcyclohexane (MCH) (Note 4) can utilize the supply chain we already have. In addition, we can produce MCH directly from renewable energy using our proprietary technology called Direct MCH🄬 (see figure below), which greatly shortens the production process.
We’re also developing technology to produce synthetic fuels (Note 5) (synthetic hydrocarbons) from hydrogen and CO₂ using renewable energy. Although electrification (the transition to electric vehicles) is progressing in the fields of automobiles and transportation, there’re some vehicles that are difficult to fully electrify, such as airplanes, large ships, and long-distance trucks. Synthetic fuels (synthetic crude oil) derived from renewable energy can be used to produce fuels such as gasoline, diesel fuel, and sustainable aviation fuel (SAF) in the same way as conventional crude oil. It can be used the same way as conventional fuel products, so it can be used by customers in their gasoline-powered cars, trucks, airplanes, and other mobility vehicles. Also, since existing infrastructure and distribution channels, such as refineries and plants, can be used as they are, it can also reduce infrastructure investment.
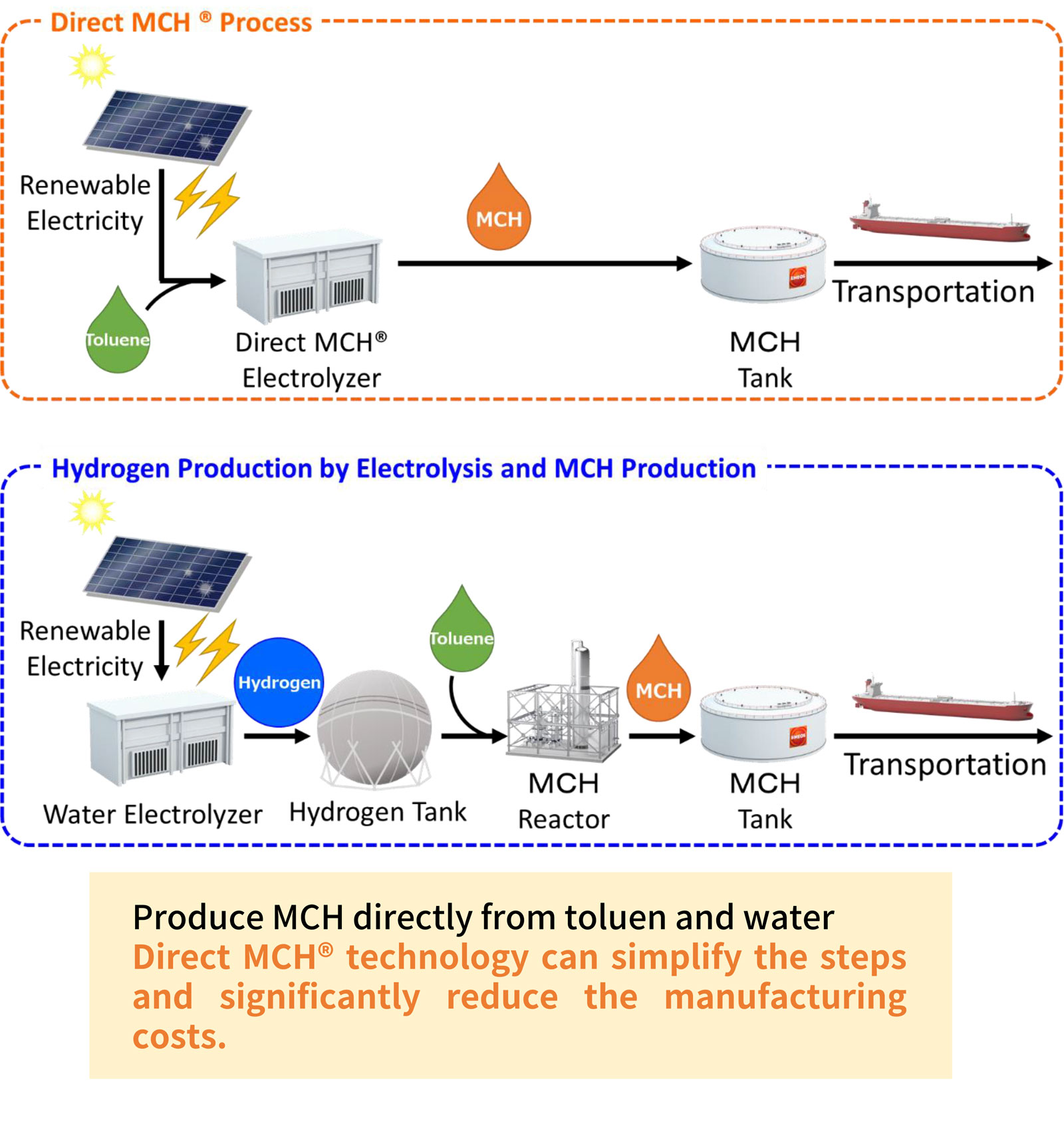
—A demonstration plant for synthetic fuels was completed in September 2024.
Fujiyama: Yes. It’s the first demonstration plant in Japan that can produce synthetic fuels from raw materials in an integrated process. It was constructed at our Central Technical Research Laboratory in Yokohama City. The plant has been in operation since September and is capable of producing 1 barrel (approximately 160 liters) of synthetic fuels per day. Part of the fuel produced by the plant will be used for a demonstration of large vehicles at the Expo 2025, Osaka, Kansai, Japan, which will start in April 2025.
—You mentioned last time that ENEOS is developing bioethanol production technology in the field of biomass using cellulose-based raw materials.
Fujiyama: ENEOS is currently conducting a demonstration project with TOPPAN Holdings for the commercialization of bioethanol (Note 6) made from used paper. Our goal is to produce bioethanol, which is attracting attention as a raw material for gasoline and SAF, from used paper considered difficult to be recycled.
—Can you tell us about technological development in initiatives for recycling and the circular economy, like you just mentioned?
Fujiyama: We’re planning to work with Bridgestone on chemical recycling used tires by using our oil refining technology. The decomposed oil from pyrolysis of used tires will be used as petrochemical raw materials from which chemicals such as butadiene, a raw material for synthetic rubber, will be produced.
We’re also working to recycle plastic waste. Highly heat-resistant plastics made through special processing are difficult to recycle. Therefore, we crush and mix them with asphalt to develop plastic-waste/asphalt pavement. Our research has shown that plastic-waste/asphalt pavement reduces CO₂ emissions by about 40% compared to conventional asphalt pavement (see figure below). We’re currently conducting a pilot project using this plastic-waste/asphalt pavement at AEON Retail’s new eco-friendly store Soyora Hamamatsu Nishiiba in Hamamatsu City, Shizuoka Prefecture, among other locations.
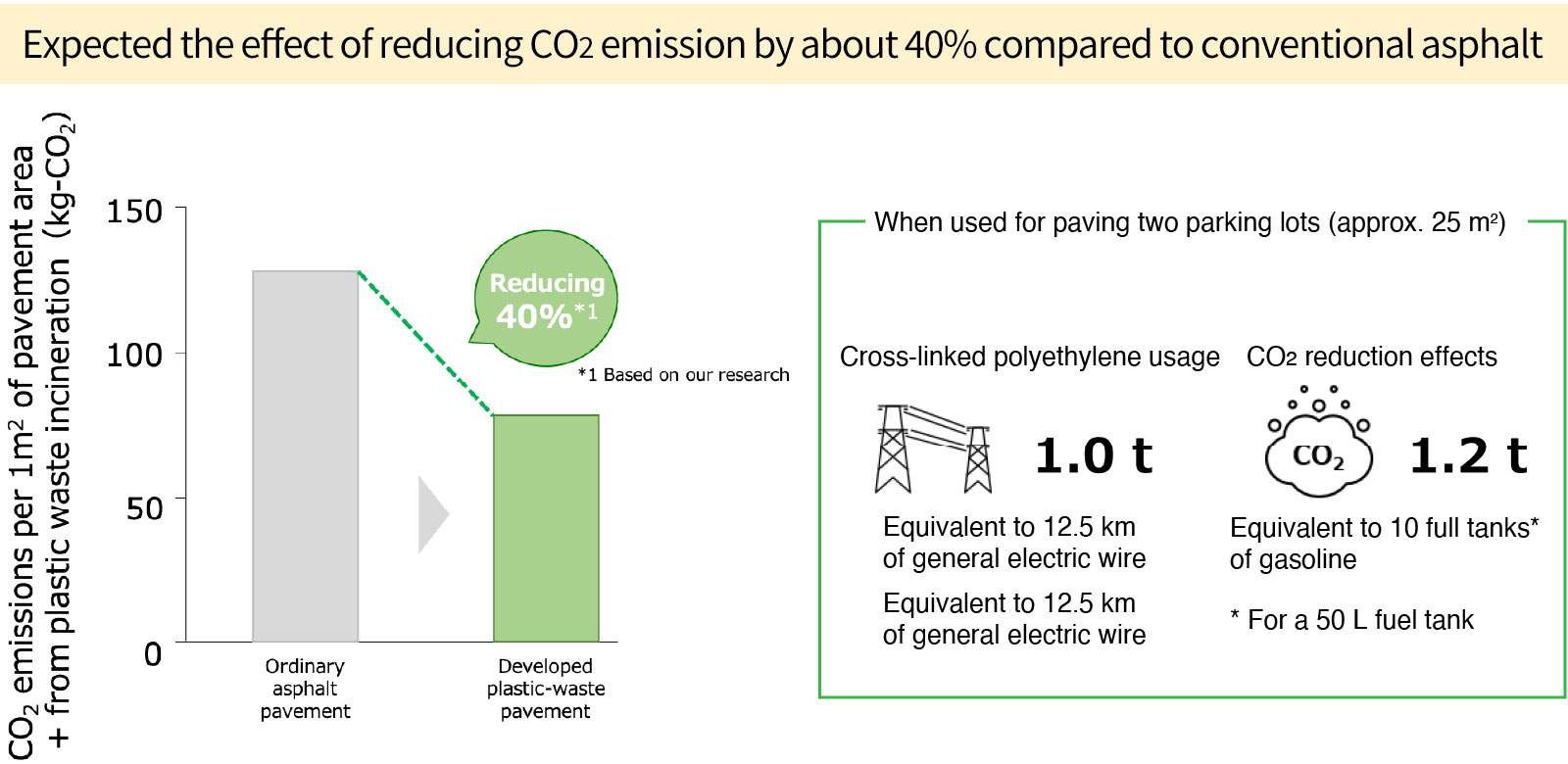
—The ENEOS Group also supplies materials such as synthetic rubber and battery materials. How are things going in terms of technological development to ensure a stable supply of materials?
Fujiyama: Materials such as synthetic rubber and battery materials are mainly handled by ENEOS Materials. These materials are hydrocarbons, just like the fuels and chemicals I’ve talked about so far, and what’s important is how they’re made. The only way to continue supplying them to the world while achieving carbon neutral is to make use of renewable energy, biomass, and CCS, which I mentioned last time. We’ve also begun research on producing plastics from biomass with the aim of establishing technologies for this purpose. We can also produce chemical raw materials from the synthetic fuels (synthetic crude oil) that I mentioned earlier, and we believe it’s possible to supply them to our business partners in the same way that we do today with petroleum-derived raw materials.
— Is the ENEOS Group taking on any other unique technological development?
Fujiyama: Digital plays a pivotal role in the ENEOS Group’s technological development. Among a variety of digital strategies we are developing, I’ll discuss some of the technology-related aspects.
We’re developing several technologies, such as automated plant operation, in collaboration with Preferred Networks (PFN), an artificial intelligence (AI) venture company. We envision replacing parts that were previously operated by human experience and intuition with AI. Some equipment can already be operated 100% by AI.
—I didn’t realize that automated plant operation had progressed so much! I can really feel the potential of AI.
Fujiyama: We’re also collaborating with PFN on materials informatics (MI). MI is a method of designing new materials by using AI to analyze vast amounts of materials data. It’s expected to greatly streamline and speed up the development of materials, which had previously relied on the experience and intuition of researchers.
We’ve developed Matlantis™ (see figure below), an ultrahigh-speed atomistic simulator, in collaboration with PFN. It can perform simulations in as little as 0.3 seconds, instead of the two months it would’ve taken in the past. This has greatly reduced the initial screening time when selecting materials.
Matlantis™ is also sold as software as a service (SaaS) through Preferred Computational Chemistry, a joint venture with PFN and Mitsubishi Corporation, and is used by many companies and research institutes both in Japan and overseas as well.
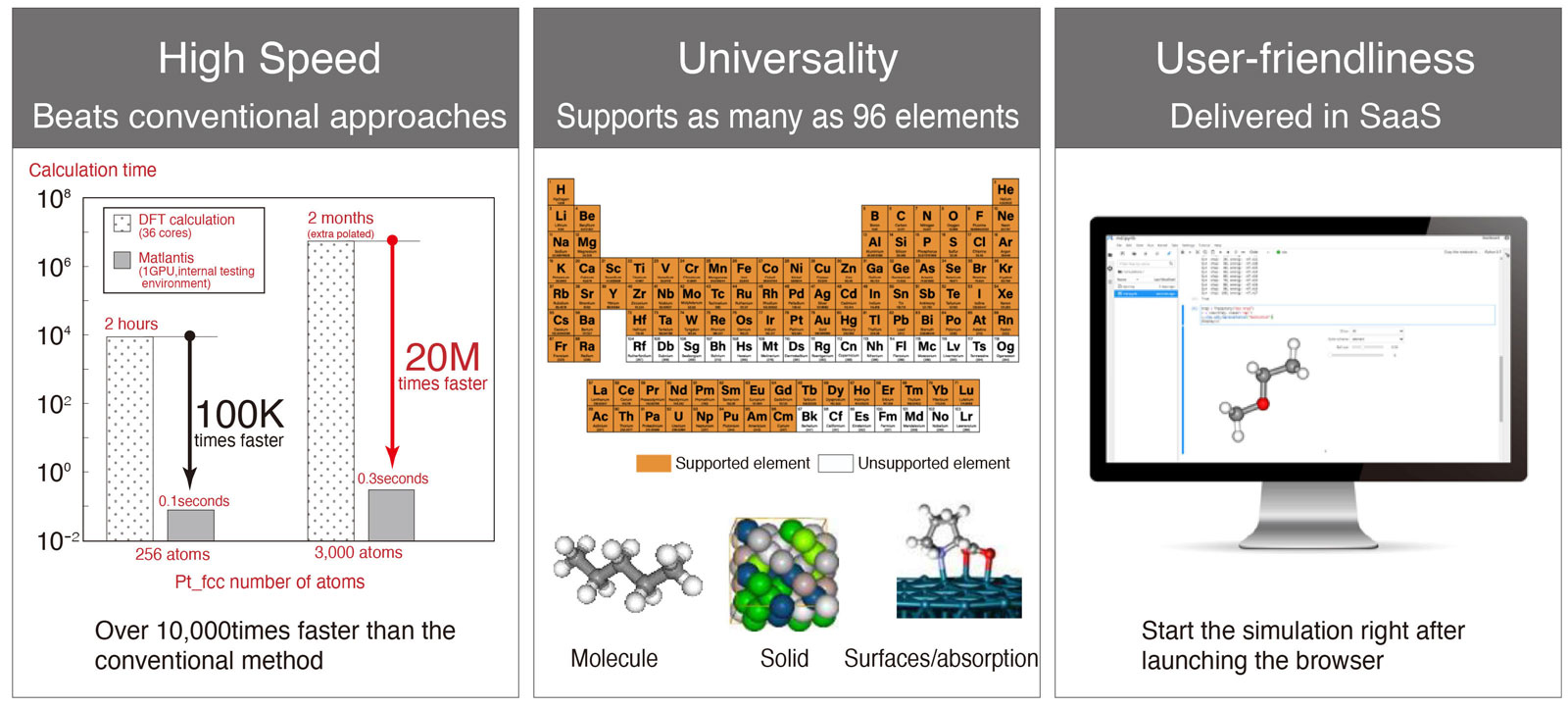
—So it’s a highly versatile model that has been widely used in other industries.
Fujiyama: Yes. The ENEOS Group is also engaged in organic-type catalysts (Note 7) for pharmaceutical production, and in June 2023 we licensed the technology for three catalysts to a major reagent manufacturer. We’re also using MI for this research and development, so the number of licensed catalysts is increasing rapidly.
—It seems like the ENEOS Group has a corporate culture that encourages taking on these kinds of challenges.
This article introduced technologies that the ENEOS Group is proud of, such as MCH production technology for hydrogen transportation, synthetic fuels production technology, and recycling technology for used tires and waste plastics. The Group has also realized automated plant operation using digital technology and acceleration of the materials development using AI. The next part will delve into the Group’s development and innovation capabilities. Please look forward to it.
Part 1: The ENEOS Group’s Technological Strategy to Achieve Carbon Neutrality
Part 3: The ENEOS Group’s Innovation Capabilities and the Need for International Cooperation
Note 4
Methylcyclohexane (MCH):
MCH is a liquid made by adding hydrogen to toluene. It contains 500 times more hydrogen per volume than hydrogen gas, so it is attracting attention as a hydrogen carrier that can efficiently store and transport hydrogen. It has properties similar to petroleum and has the advantage that existing petroleum infrastructure can be used for storage and transportation. It is usually used as a solvent or fuel, and is also used as a solvent in correction fluid.
Note 5
Synthetic fuels:
This refers to artificial petroleum substitute fuels produced from hydrogen and CO₂. Synthetic crude oil is a mixture of hydrocarbons like conventional crude oil, which can be made into fuel products such as gasoline, diesel oil, and SAF depending on the application. As it is produced from pure CO₂ and H2, unlike conventional crude oil, it does not contain impurities such as heavy metals and sulfur compounds, and thus has a lower environmental impact.
Note 6
Bioethanol:
This refers to ethanol made by fermenting biomass. It can be used as automobile fuel, and in Japan, a certain amount is legally required to be blended with gasoline. The main type of bioethanol currently in circulation is ethanol derived from sugarcane or corn imported from overseas, but ENEOS has developed a technology to produce ethanol from woody biomass (trees), which is used as a raw material for paper. ENEOS is also working to produce ethanol from used paper using this technology.
Note 7
Organic-type catalysts:
A general term (coined word) for organic molecular catalysts and organometallic catalysts. Organic molecular catalysts are low-molecular-weight compounds that do not contain metal elements and are composed of elements such as carbon, hydrogen, oxygen, nitrogen, sulfur, and phosphorus, and act as catalysts. Organometallic catalysts contain metal elements as well. Compared to conventional metal catalysts, they are attracting attention as “environmentally friendly catalysts” because they do not use heavy metals. In recent years, the restrictions gets stricter on the amount of metal contained in catalysts used in the manufacture of pharmaceuticals, and ENEOS is working to develop organic-type catalysts that can demonstrate performance and cost competitiveness equivalent to or better than existing catalysts while responding to the strengthening of regulations.