The 3Rs (Reduce, Reuse, Recycle)
Basic Approach
The ENEOS Group is doing its part to develop a recycling-oriented society by reducing waste and recycling resources in its own activities as well as in society. The Group is expanding its recycling business, and applies the 3Rs—reduce, reuse and recycle—to ensure that it uses resources efficiently.
Structure
For information on our structure, see Environmental Management.
Material Issues, Plans and Results
Fiscal 2023 Targets, Results and Progress
Evaluation: Achieved/Steady progress Not achieved
Material ESG Issue | Initiative | Target (KPI) | Results/Progress | |
---|---|---|---|---|
Contribution to the development of a recycling-oriented society | Reduction in landfill disposal | Waste-to-landfill ratio: Maintain zero emissions (less than 1%) | 1.2% |
Results
- For information about , see the Editorial Policy.
Landfill Disposal Volume and Waste-to-Landfill Ratio
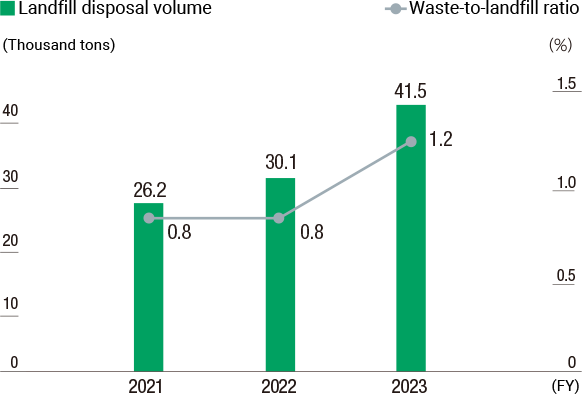
- Note:
- For detailed data, see Data.
Major Initiatives
Waste Reduction
The Group manages and recycles waste appropriately, with a target of maintaining zero emissions (waste-to-landfill ratio of less than 1%).
In fiscal 2023, waste totaled 3,482 thousand tons and landfill waste totaled 41 thousand tons. The waste-to-landfill ratio was 1.2%, indicating that we did not achieve our zero-emissions target. Factors that contributed to the increases in total waste and waste-to-landfill ratio from the previous fiscal year included an increase in building demolition work and pavement repair work in construction projects.
Sludge is the most common waste generated by refineries and plants, accounting for about 40% of the total waste volume. We pursue recycling and reuse through initiatives for waste reduction, including using the collected particulate matter and sludge released from oil refineries as raw materials for cement, and the repeated use of neutralized sludge1 at our smelting and refining facilities. In addition, we use LCA methodology2 in evaluating the development of certain lubricant products.
- 1Material generated by the neutralization reaction in the smelting process.
- 2LCA methodology involves quantitatively evaluating the environmental effects of product manufacturing throughout the entire life cycle, from procurement of raw materials to manufacturing, transport, use, and disposal. LCA is an acronym for “life cycle assessment.”
Targets and Processes Surpassing Legal Requirements for Industrial Waste
In response to Keidanren’s (Japan Business Federation) call for the development of a recycling-oriented society, petroleum companies have been working on waste reduction and recycling at their refineries. The target for the petroleum industry in Keidanren’s Voluntary Action Plan for Establishing a Sound Material-Cycle Society is to maintain a waste-to-landfill ratio of 1% or less in fiscal 2025. ENEOS is striving to reduce the waste-to-landfill ratio by setting a target to maintain “zero emission plus” (waste-to-landfill ratio of less than 0.3%), which is more rigorous than the Keidanren target.
Responsible Management of Waste
We confirm whether waste emitted at our refineries is disposed of responsibly in accordance with our duty under the Waste Disposal and Public Cleansing Act. Each of our refineries systematically conducts audits of waste disposal contractors.
Increasing the Use of Recyclable Raw Materials
The Group is working to reduce its use of raw materials by streamlining production and expanding the use of recyclable raw materials.
JX Advanced Metals promotes the effective use of resources by efficiently recovering copper, precious metals, and rare metals from recyclable raw materials, drawing from processes that utilize its smelting technology, developed over the course of more than a century. The company has established a long-term goal of increasing the use of recyclable raw materials in copper smelting to 50% (ratio in raw materials or ratio contained in products).
In fiscal 2023, 230 thousand tons of the 1,627 thousand tons of raw materials used in the company’s business activities were recycled resources.
Launching 100% Recycled Electrolytic Copper Applying the Mass Balance Method
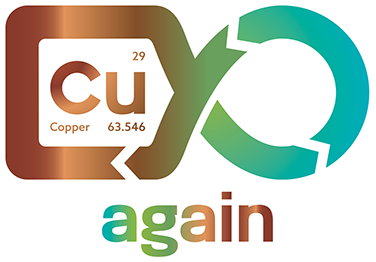
In January 2024, JX Advanced Metals announced that it will launch two types of 100% recycled electrolytic copper applying the mass balance method*: PCL100/mb (Partnered Closed Loop 100% mass balance method) and MR100/mb (Mixed Recycle 100% mass balance method) in fiscal 2024.
With PCL100/mb, the equivalent amount of copper contained in recycled raw materials, such as those derived from end-of-life products collected by the customer, is returned as 100% recycled electrolytic copper. MR100/mb supplies 100% recycled electrolytic copper from recycled raw materials collected from the market through the JX Advanced Metals Group’s recycled raw material collection network.
Both of these are the first attempts in the domestic copper refining and smelting industry. PCL100/mb in particular is an advanced proposal in which the company and its customers co-create solutions to the social issues of resource recycling and decarbonization.
JX Advanced Metals has also launched the “Cu again” project, an initiative aimed at the social implementation of 100% recycled electrolytic copper, to co-create domestic resource recycling with its customers.
- * When raw materials with different properties are mixed, this method allocates these properties to certain parts of products according to the input ratio of the raw material with a certain property.
Human Resource Development in Nonferrous Smelting, Refining and Recycling
In recent years, the number of researchers and engineers in fields related to nonferrous smelting, refining and recycling has been steadily decreasing in Japan. In response, JX Advanced Metals has collaborated with the Institute of Industrial Science of the University of Tokyo to launch the Endowed Research Unit for Nonferrous Metal Resource Recovery Engineering (JX Metals Endowed Unit) to combine the forces of industry, academia and government to reenergize and raise the level of activity in the industry. The Unit is using industry-academia collaboration to advance various initiatives to cultivate human resources to develop and apply smelting and refining technologies in the nonferrous base metals and rare metals fields. In fiscal 2023, the Symposium on Challenges and Initiatives for Talent Acquisition and Development in the Domestic Manufacturing Industry was held in September. The symposium covered the current status of retaining and developing human resources by nonferrous metals companies and endowed courses, and featured a panel discussion.
Researching Rare Metal Recycling from Lithium-Ion Batteries
JX Advanced Metals began recycling rare metals contained in lithium-ion batteries in 2009.
In 2020, it installed bench-scale equipment (continuous small-scale testing equipment) at the Technology Development Center of Hitachi Works. Since then, JX Advanced Metals has been working on technological development for closed-loop recycling, where rare metals are recovered from used automotive lithium-ion batteries and reused as raw materials for new ones. To verify this technology, in May 2021 the company established JX Metals Circular Solutions Tsuruga Co., Ltd., which is conducting verification tests using recovery facilities for high-purity nickel sulfate (2021), high-purity cobalt sulfate (2022), and high-purity lithium carbonate (2023). These initiatives were selected in April 2022 for the Green Innovation (GI) Fund Projects1 of the New Energy and Industrial Technology Development Organization (NEDO).
In August 2021, JX Advanced Metals established JX Metals Circular Solutions Europe GmbH (JXCSE) in Germany to advance the commercialization of lithium-ion battery recycling, with an eye on collaboration with European automakers. JXCSE has participated in the “HVBatCycle” research consortium, supported by Germany’s Federal Ministry for Economic Affairs and Climate Action (BMWK), since January 2022 through TANIOBIS GmbH, a JX Advanced Metals Group company also based in Germany. As part of the consortium, JXCSE installed bench-scale equipment2 on the TANIOBIS premises in Goslar, where it began operations in March 2023 to verify closed-loop recycling using its technologies.
- 1Projects in which the government provides continuous support for 10 years to companies and other organizations working on management issues toward carbon neutrality by 2050 in Japan, from R&D and demonstration to social implementation.
- 2Bench-scale equipment (continuous small-scale testing equipment) that recovers high-purity rare metals from pulverized batteries (black mass) in various forms (liquids, salts, metals) by solvent extraction method.
Pursuit of a Circular Economy
The Group is promoting a circular economy1 for the realization of a recycling-oriented society that does not rely on conventional resources.
The world is shifting from a linear economy2 to a circular economy—from a mass production, mass consumption economy to an economy that recycles and reuses resources. A circular economy goes one step further than the 3Rs by considering the environment from the design stage, using maintenance to lengthen product life, and enhancing usage efficiency by incorporating leasing and sharing.
Products supplied to society generate CO2 in each stage of the life cycle, from procurement of resources to manufacturing, sales, use, and disposal. Creating a cycle where manufactured products are recycled instead of being disposed of can help to lower these CO2 emissions.
The Group is helping to realize a circular economy, and by extension a carbon-neutral society, in the materials and services field by shifting to non-fossil raw materials and developing sharing businesses.
- 1An economic system that seeks to recycle resources through their effective use in each stage of the value chain
- 2An economic system where products flow in a single direction with resources being consumed and disposed without recycling or reuse
Efforts for a Circular Economy to Realize Circulating Society Independent from Conventional Resources
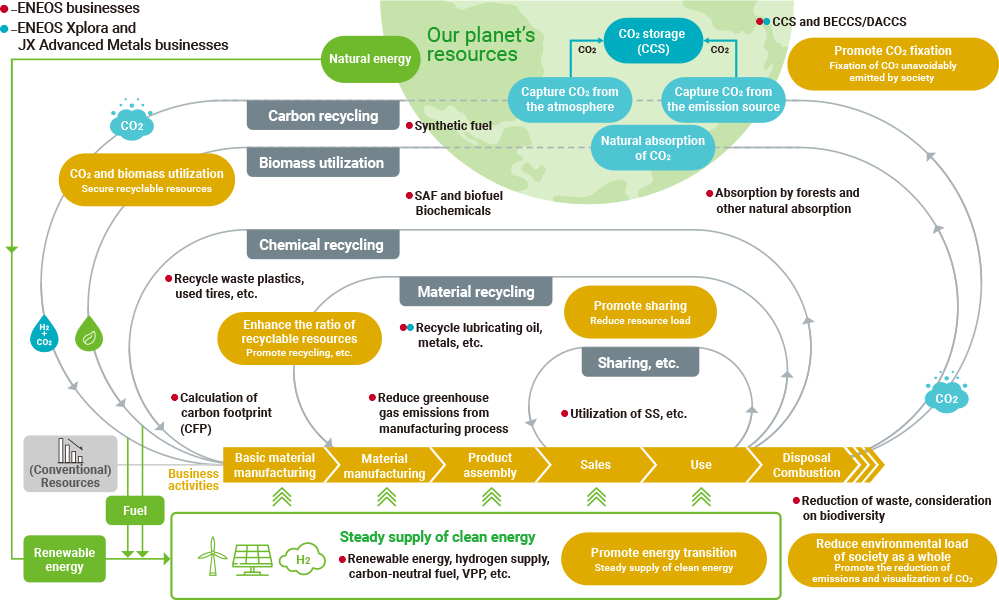
Joint Plastic-to-Oil Conversion Business (Chemical Recycling)
ENEOS is engaged in a joint plastic-to-oil conversion business with Mitsubishi Chemical Corporation at the Kashima industrial complex, site of the Kashima Refinery. The two companies are currently constructing a commercial chemical recycling facility with an annual processing capacity of 20,000 tons, which will be the largest-scale in Japan on a commercial basis. The recovered oil produced at the facility will be used as a raw material at both companies’ petroleum refinery and naphtha cracker to produce recycled petroleum and plastic products.
Workflow of Plastic-to-Oil Conversion
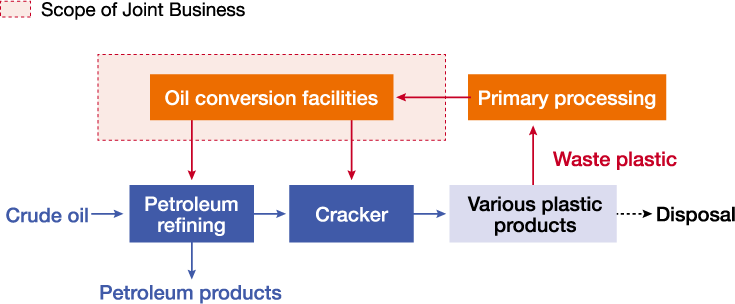
Recycling Synthetic Rubber from Used Tires (Chemical Recycling)
Synthetic rubber derived from petroleum is one of the main materials used when producing tires. ENEOS, in cooperation with Bridgestone Corporation, aims to establish chemical recycling technology to produce chemicals and other raw materials for synthetic rubber from cracked oil obtained from the precise pyrolysis of used tires. Looking to the future, ENEOS is committed to further improving resource recycling and reducing CO2 emissions in the value chain of the tire/rubber and petroleum/petrochemical industries. In February 2022, this initiative was adopted as a Green Innovation Fund Project of the New Energy and Industrial Technology Development Organization (NEDO), a national research and development agency.
Collection of Used PET Bottles at Service Stations and Demonstration of Recycling Chains (Chemical and Material Recycling)
Since April 2023, ENEOS, in cooperation with Suntory Holdings Limited and Kyoei Sangyo Co., Ltd. has been conducting a demonstration test to collect and recycle used PET bottles at ENEOS service stations in Kawasaki City and Utsunomiya City. Through this test, we are verifying the feasibility of establishing a horizontal recycling chain for collecting used PET bottles through our service station network, as well as recycling, reprocessing, and re-commercializing the bottles.
Horizontal Recycling Chain for Used PET Bottles
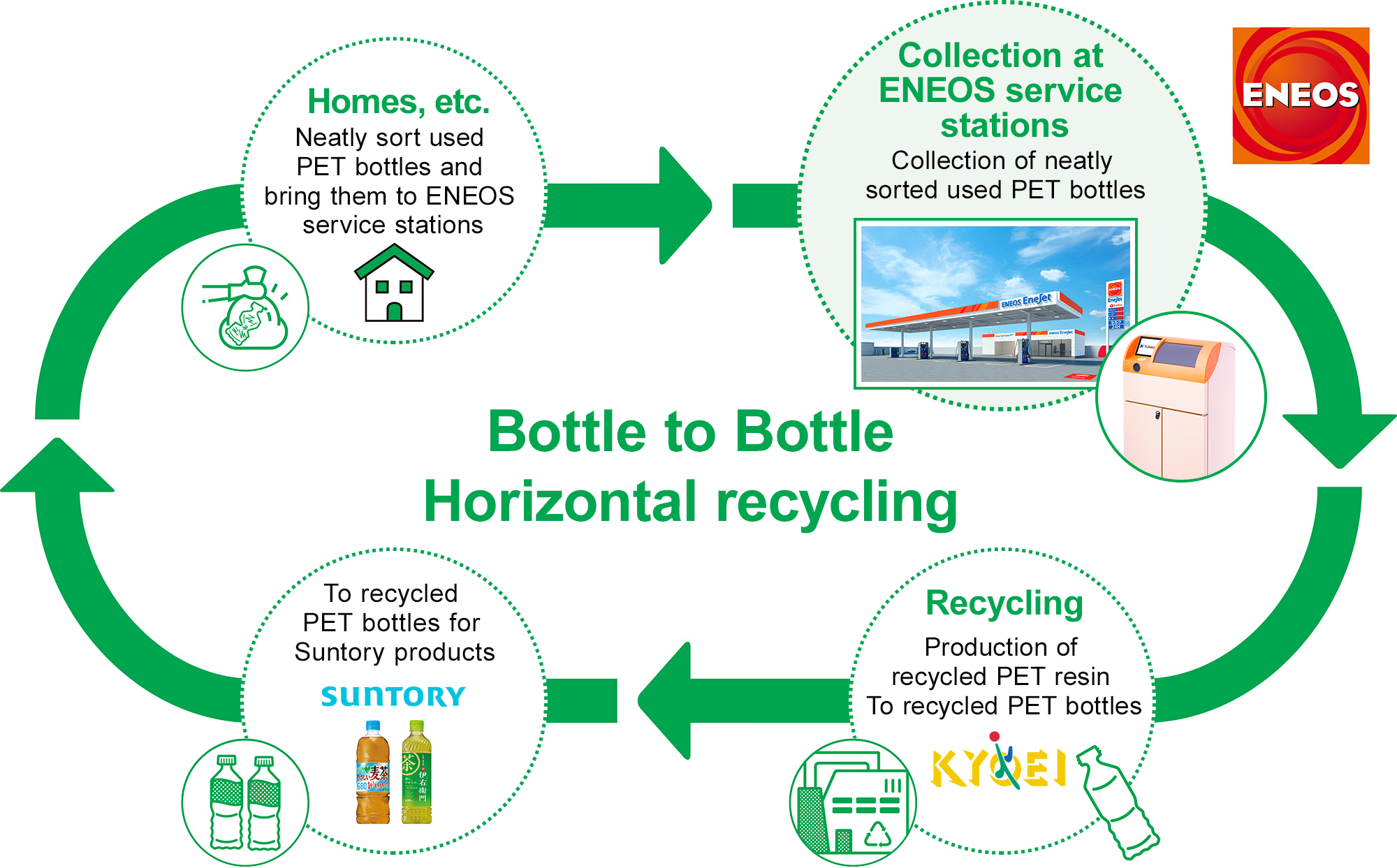
Asphalt Pavement Utilizing Waste Plastics (Material Recycling)
A typical asphalt pavement is composed of about 95% (by weight) of stones and sand called aggregates, and asphalt, called a binder, holds these aggregates together.
ENEOS is working on the development of asphalt paving technology that replaces all aggregates with waste plastic. Demonstration tests are now underway at the new SOYORA Hamamatsu Nishiiba store opened by AEON RETAIL Co., Ltd. in Hamamatsu City, Shizuoka Prefecture in October 2023, and at the ENEOS Platform opened in Ushiku City, Ibaraki Prefecture in March 2024.
Through the use of waste plastics, which are difficult to use in material recycling and are mainly used for thermal recycling, our new asphalt pavement is expected to reduce CO2 emissions by about 40% compared to conventional ones.
Using Waste Lubricants to Produce Lubricant Base Oil (Material Recycling)
ENEOS is working to commercialize a process for reusing waste lubricants in lubricant base oil. Recycling waste lubricants as base oil, which is the main base material for lubricant products, reduces CO2 emissions from lubricants throughout the entire life cycle and helps to ensure a stable supply of base oil.
This demonstration project was selected for inclusion in the Demonstration Project for a Plastic Resource Circulation System toward a Decarbonized Society, run by the Ministry of the Environment. In this two-year demonstration project, which started in fiscal 2022, we succeeded in producing low-carbon base oil. In the technical study, we use used engine oil collected from the market with the cooperation of Toyota Motor Corporation as a raw material.
Scope of Base Oil Reuse Business in the Lubricant Life Cycle
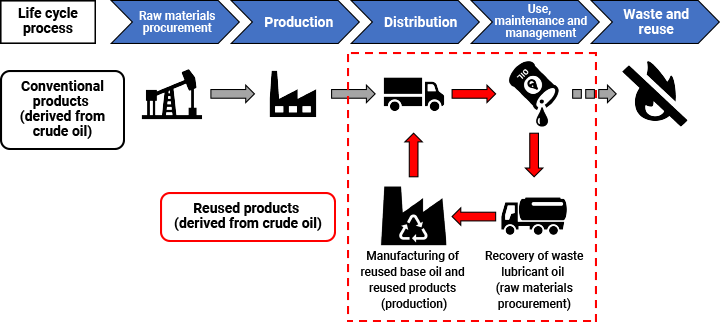
The World’s First Initiative for Bio-Paraxylene Origin “Biomass to PET Bottles” (Effective Utilization of Biomass)
In August 2023, ENEOS reached an agreement with Suntory Holdings Limited and Mitsubishi Corporation to establish a supply chain for sustainable PET resin made from bio-paraxylene. ENEOS manufactures paraxylene, a raw material for PET bottles, and has been studying the possibility of supplying chemicals made from non-fossil raw materials. In the recently established supply chain, bio-paraxylene will be produced for the first time in the world on a commercial scale from biomass feedstock made from untapped resources such as used cooking oil, using the mass balance method*, at the ENEOS Mizushima Refinery. By realizing “biomass to PET bottles” through the use of bio-paraxylene, we will increase the “non-fossil resource ratio of petrochemical feedstocks,” as stated in our Carbon Neutrality Plan.
- * A method in which raw materials with specific characteristics, such as biomass raw materials, are mixed with non-biomass raw materials in the distribution and processing process from raw materials to finished products, and those characteristics are assigned to a portion of the product in proportion to the input of raw materials with those characteristics. A system that connects the value of the characteristics of raw materials to the final product by managing the balance of In and Out for each company in the supply chain.
“Biomass to PET Bottles” Supply Chain
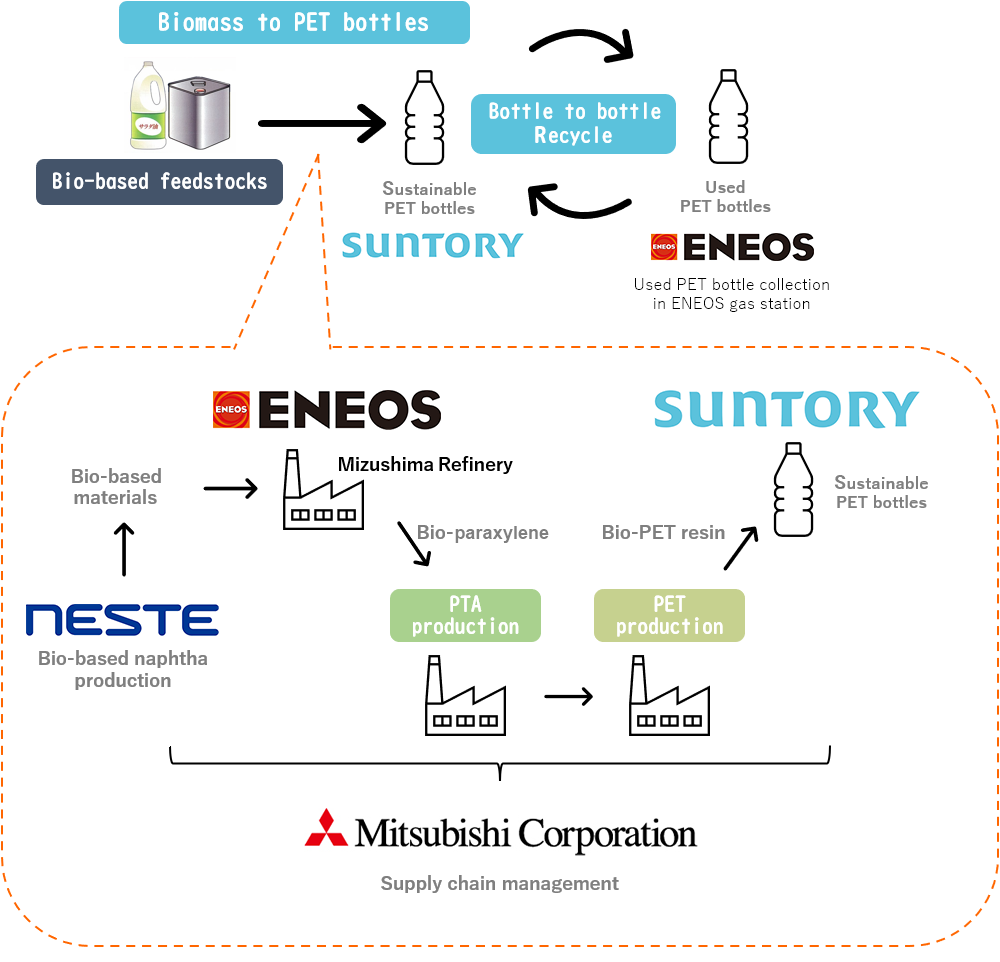
Battery Recycling Through Sharing Services (Sharing)
ENEOS service stations are working to recycle batteries. In 2022, we established Gachaco, Inc.*, which provides battery sharing services for electric motorcycles. Gachaco has established battery exchange sites at 50 ENEOS service stations, mainly in Tokyo and Osaka, and is working to build a system for the recycling of batteries.
- *A joint venture of ENEOS Holdings, Honda Motor Co., Ltd., Kawasaki Motors, Ltd., Suzuki Motor Corporation, and Yamaha Motor Co., Ltd.
Smelting, Refining and Recycling Businesses
JX Advanced Metals is engaged in an integrated range of businesses related to nonferrous metals such as copper, precious metals and rare metals. These organically related businesses encompass resource development, smelting and recycling, and the provision of high-value-added materials, such as electronic materials. Smelting and recycling, which act as “veins” and “arteries” of this value chain, include the following three businesses.
- Smelting and Refining business: Recovery of metals by smelting and refining ore extracted from mines
- Recycling business: Recyclable raw materials are melted utilizing reaction heat from the smelting and refining process for the recovery of metals and reuse as raw materials
- Environmental Services business: Detoxification of industrial waste
Utilizing the key features and strengths of smelting and recycling, including zero emissions, proprietary treatment processes based on smelting and refining technologies, and a global collection network, JX Advanced Metals contributes significantly to the development of a sustainable, recycling-oriented society.
Key Features and Strengths of the Smelting and Recycling Businesses
1. Zero Emissions
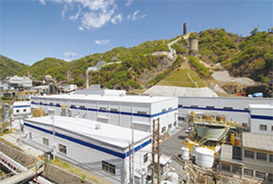
JX Advanced Metals is pursuing zero emissions, where no secondary waste that requires landfill disposal is produced, in both its smelting and refining business and its recycling business. Iron and other ferrous metals other than nonferrous metals are recovered as slag and used as raw materials for cement and other purposes. By preventing the generation of secondary waste, we are reducing our environmental impact.
2. JX Advanced Metals’ Proprietary Treatment Processes Based on Smelting and Refining Technologies
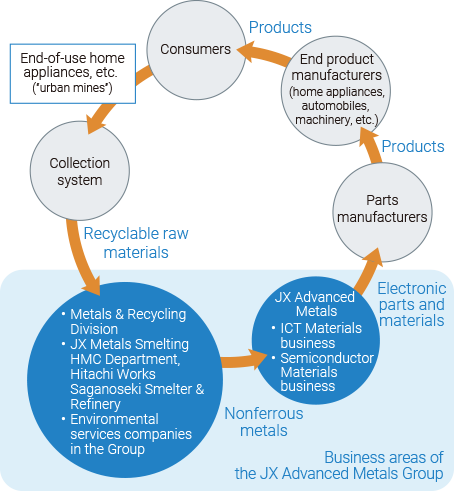
JX Advanced Metals carries out recycling of nonferrous metals in its recycling business using efficient and reliable proprietary treatment processes based on technologies developed over many years through its operations at mines, smelters, and refineries.
At the JX Metals Smelting Saganoseki Smelter & Refinery, which boasts Asia’s largest treatment capacity for recycling copper and precious metals, energy is conserved by using the reaction heat generated during the copper concentrate smelting process for melting recyclable raw materials.
3. Global Collection Network
To advance its recycling business, JX Advanced Metals is focusing on boosting the collection of recyclable raw materials at its locations in Japan and overseas and increasing the processing capacity of its copper smelting and refining facilities. In fiscal 2021, a new collection site was established at JX Metals Smelting Saganoseki Smelter & Refinery (Oita Prefecture) to increase pre-processing capacity. Outside of Japan, in addition to existing collection and pre-treatment facilities in Taichung (Taiwan), along with collection support facilities in Arizona (United States) and Frankfurt (Germany), in fiscal 2022, JX Advanced Metals acquired eCycle Solutions Inc. (Canada), marking its entry into the collection, disassembly, and sorting business for electrical and electronics waste. Recyclable raw materials collected in Japan and abroad, along with raw materials collected by Group companies in Tomakomai (Hokkaido), Mikkaichi (Toyama Prefecture), and Shirakawa (Fukushima Prefecture), are sent to and undergo pre-processing in Hitachi (Ibaraki Prefecture) and at the Saganoseki Smelter & Refinery, and metals from these materials are recycled and recovered at the Saganoseki Smelter & Refinery.