Basic Approach
As a corporate group responsible for the stable supply of energy and materials, the ENEOS Group believes that ensuring safe operations is the basis of our business survival and social credibility, as well as the source of our competitive edge.
Based on this understanding, safety has been prioritized in the ENEOS Group Philosophy, and our basic policy on safety and security has been stipulated in the ENEOS Group Code of Conduct.
Based on the above, each Group company has established its own safety policy in accordance with its business characteristics and assesses risks pertaining to occupational safety, thereby ensuring multiple layers of effective safety activities. Specifically, we aim to enhance our safety activities and safety training programs, in which the employees of our contractor companies also participate, and we have established preventive and emergency measures to cope with all manner of accidents, problems and natural disasters.
We check with our labor unions to make sure efforts are being made to maintain the facilities needed to ensure the health and safety of labor union members (Article 90 of the Ancillary Agreement to the Labor Agreement).
ENEOS Group Code of Conduct (excerpt)
- 2.Safety and security
- (1)We regard safety and security as the foundation of our business activities, set high safety and security standards, always ensure safety and security, and take appropriate measures to prevent any incidents and injuries.
- (2)We have established preventive and emergency measures to minimize damage to our business sites caused by natural disasters, including earthquakes. We also make every effort to protect the lives and safety of our directors, officers and employees, communities, and others concerned.
- (3)We shall not work under the influence of alcohol or drugs, when ill, or under other conditions where safety cannot be ensured.
ENEOS Group Safety Policies
Each ENEOS Group company has established a policy on occupational health and safety which states its commitment to prioritizing and fully ensuring the safety of its workers.
- ENEOS
We aim to ensure that nobody gets hurt and to eliminate accidents. - ENEOS Xplora
Ensuring that Health, Safety and Environment (HSE) considerations are given prevailing status over our other business considerations. - JX Advanced Metals
We place the highest priority on ensuring the health and safety of people working in all areas of business operations.
See the following for further details on the safety policies of the Group’s principal operating companies.
Structure
For information about our structure, see ESG Management Structure.
We have established the ENEOS Group Safety, Health & Environment Council, chaired by the officer responsible for the Safety, Health & Environment Department at ENEOS Holdings. The council meets, in principle, twice annually, to share information on the status of occupational injuries and the implementation of safety activities at the Company and its principal operating companies, as well as to discuss and develop measures to prevent occupational injuries.
Operation of Safety Management System and Status of Certification
Each Group company has built safety management systems tailored to its respective business characteristics. Our companies are continuously making efforts to raise safety awareness and prevent occupational injuries through means such as implementing regular safety education and training, conducting investigations into the causes of incidents and formulating and implementing measures to prevent recurrence.
ENEOS has established and implemented its own safe operations management system (SOMS), which conforms to ISO standards, at all of its refineries and plants.
ENEOS Xplora has adopted its own HSE1 management system (HSEMS), which conforms to ISO standards. Through HSEMS system management, the company has established an integrated safe operations framework that includes overseas business sites.
JX Advanced Metals is moving ahead with the acquisition of ISO 450012 and JIS Q 451003 certification, and by March 2024, 13 domestic business sites had obtained certification. The remaining business sites, including those that have newly joined the JX Advanced Metals Group, plan to acquire certification in fiscal 2024 and beyond.
- 1Acronym for “health, safety and environment”
- 2An international standard for occupational health and safety management systems
- 3JIS standard based on the international standard ISO 45001, with additional requirements particular to Japan
Material Issues, Plans and Results
Fiscal 2023 Targets, Results and Progress
Evaluation:Achieved/Steady progressNot achieved
Material ESG Issue | Initiative | Target (KPI) | Results/Progress | |
---|---|---|---|---|
Ensuring safety / Health enhancement | Reduction in occupational injuries | Zero serious occupational injuries (occupational fatalities) | Zero | |
TRIR*of 1.0 or less * Number of occupational injuries per million working hours (non-lost-time occupational injuries + lost-time occupational injuries and fatalities) |
0.94 |
Results of Major Initiatives for Ensuring Safety
The ENEOS Group prioritizes and is fully committed to the safety of its workers. We have set material targets for zero serious occupational injuries (occupational fatalities) and a total recordable incident rate (TRIR)* of 1.0 or less, and we implement comprehensive safety activities and safety training for employees, including those of contractor companies.
In fiscal 2023, we had zero serious occupational injuries (occupational fatalities) and TRIR of 0.94, thus achieving our material targets for the second year in a row. We believe that the achievement of these targets attests to the firm establishment of our safety activities.
However, 40 workers, including employees of contractor companies, sustained lost-time occupational injuries. This was an increase from the 29 workers in the previous fiscal year, and improvement is still necessary. As most of these injuries occurred in the course of work activities, we will examine and continue implementing our ongoing safety activities to reduce the number of injuries. We have also found that a certain number of accidents occur outside of work, such as when moving from one place to another. As a preventive measure for accidents that occur outside of work, we seek to raise safety awareness by sharing situation analysis and cause investigation results for individual incidents.
As a company group that provides work environments for a large number of employees, including those of contractor companies, we will continue to implement effective safety activities in accordance with the characteristics of our businesses as part of our efforts to eliminate occupational accidents.
- *Total recordable incident rate (TRIR) is the number of occupational injuries per million working hours (non-lost-time occupational injuries + lost-time occupational injuries and fatalities)
- For information about , see the Editorial Policy.
Occupational Injuries
(Persons)
FY2021 | FY2022 | FY2023 | |||
---|---|---|---|---|---|
Number of occupational injuries | Directly hired employees | Fatalities | 0 | 0 | 0 |
Lost work time | 17 | 12 | 19 | ||
Subtotal | 17 | 12 | 19 | ||
Contractors (contractor companies, etc.) |
Fatalities | 0 | 0 | 0 | |
Lost work time | 26 | 17 | 21 | ||
Subtotal | 26 | 17 | 21 | ||
Total | 43 | 29 | 40 |
- Note:
- Scope of occupational injury statistics: ENEOS, ENEOS Xplora and JX Advanced Metals
Occupational Injury Frequency Rate*
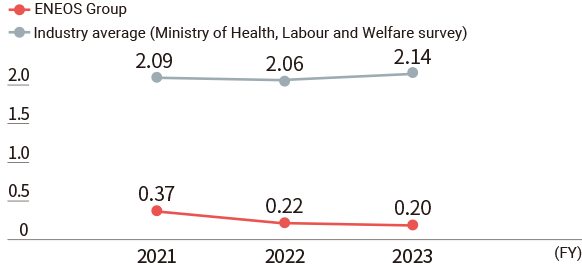
- Notes:
- Scope: The refineries, plants and business sites of ENEOS, ENEOS Xplora and JX Advanced Metals (For details, see Data).
- *Frequency rate: The number of injuries and fatalities per million cumulative hours worked; indicates the frequency of occurrence of occupational injuries.
Definition of terms by the Ministry of Health, Labour and Welfare (Available in Japanese only)
Occupational Injury Severity Rate*
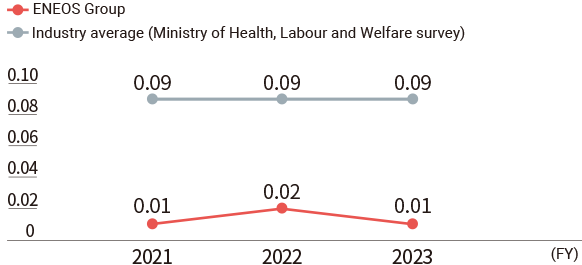
- Notes:
- Scope: The refineries, plants and business sites of ENEOS, ENEOS Xplora and JX Advanced Metals (For details, see Data).
- *Severity rate: The aggregated number of working days lost per thousand cumulative hours worked; indicates the severity of occupational injuries.
Definition of terms by the Ministry of Health, Labour and Welfare(Available in Japanese only)
TRIR and LTIR
(Persons)
Item | FY2021 | FY2022 | FY2023 | |
---|---|---|---|---|
Total recordable incident rate (TRIR) |
Directly hired employees | 1.13 | 1.00 | 0.94 |
Contractors (contractor companies, etc.) | 2.13 | 2.59 | 2.45 | |
Lost time injury rate (LTIR) |
Directly hired employees | 0.26 | 0.19 | 0.15 |
Contractors (contractor companies, etc.) | 0.72 | 0.51 | 0.45 |
- Notes:
- Scope: ENEOS Holdings, ENEOS head office and 11 refineries and plants, ENEOS Xplora head office and 4 business sites, JX Advanced Metals head office and 5 business sites (For details, see Data).
- TRIR: Number of occupational injuries per million working hours (non-lost-time occupational injuries + lost-time occupational injuries and fatalities), excluding heat stroke (first aid)
- LTIR: Number of lost-time occupational injuries and fatalities per million working hours
Major Initiatives
Increased Scope of Data for TRIR and LTIR
As part of the management of safety-related targets, the principal operating companies use TRIR and LTIR as indicators. In fiscal 2022, we decided to expand the scope of data for TRIR and LTIR.
In addition to the original scope of data, which includes company employees and employees of contractor companies at business sites under the direct control of the principal operating companies, the expanded scope of data will also cover the group companies of each of the principal operating companies. We started collecting data in fiscal 2024.
Safety Activities
Group companies are working to raise safety awareness and enhance safety management. Risks at production and manufacturing sites are managed using a PDCA cycle to identify hazards, assess risks and take necessary risk mitigation measures and assess their effectiveness.
Every year in July, ENEOS releases a video message on safety by its president to all employees, demonstrating the company’s commitment to safety. At its refineries and plants, the company has implemented a behavior-based safety (BBS) system that is used to facilitate safe operations by focusing on individual behavior.
ENEOS Xplora has implemented various safety activities at its business sites both overseas and in Japan. For example, workers have stop work authority (SWA) so that anyone can halt work in the event of unsafe behavior. Furthermore, we encourage the active participation of frontline workers in safety to help raise the safety awareness of the entire workforce, through activities such as Unsafe Condition Unsafe Act (UCUX), where workers can point out or propose improvements at any time to resolve unsafe conditions or behaviors.
JX Advanced Metals conducts training to improve the skills of foremen at each business site and promotes the development of key frontline personnel, thereby continuously working to improve safety awareness and risk sensitivity through communication. In addition, by providing training to improve abilities for conducting workplace patrols, mainly for managers, the company is working to develop people who do not overlook dangers in the workplace.
Group-wide Safety Action Items
In order to prevent serious occupational injuries, we designated preventing falls, separating people from heavy machinery, and preventing heatstroke as the three safety action items for the three principal operating companies*. We established these action items in the ENEOS Group guidelines in February 2020.
Since fiscal 2021, we have reflected the three safety action items, positioned as common issues for the three principal operating companies, into the safety activities of each company. The principal operating companies are also sharing safety initiatives with their own group companies as part of their efforts to eliminate occupational injuries.
- *ENEOS, ENEOS Xplora and JX Advanced Metals
Group-wide Safety Action Items
- Preventing falls
- Separating people from heavy machinery
- Preventing heatstroke
Hazard Simulation Training Using Virtual Reality
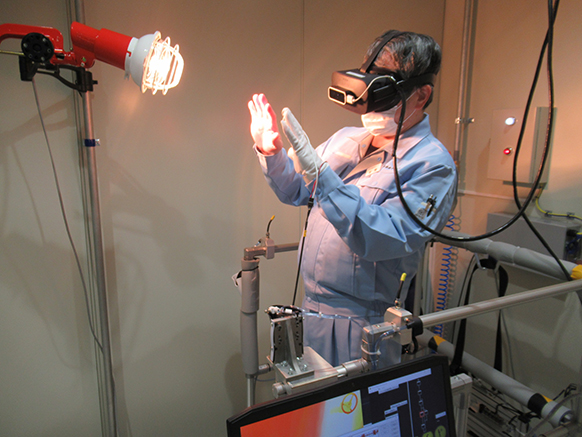
The ENEOS Group launched the ENEOS Group Safety Education Center in Hitachi City, Ibaraki Prefecture in 2013 to enable workers to learn about the hazards inherent in day-to-day operations through simulated experiences. Since fiscal 2017, the center has implemented a training program unique to the Group using virtual reality (VR) technology.
The program enables workers to feel what it is like to be involved in an accident and think about victims’ psychological state, as well as accident causes and preventive measures.
Using VR technology, trainees can experience simulated accidents that cannot be safely replicated in the real world, such as steam explosions, being struck by heavy machinery, getting caught in rotating equipment, and falling from heights. These experiences improve their ability to detect workplace hazards to avoid or deal with when they occur. Since the launch of the program, VR experiences with scattering of chemicals, getting fingers caught in slings, grinder recoil, falling down stairs, electric shock, fire caused by static electricity, falls from temporary scaffolding, making contact with heavy machinery, getting caught in conveyor belts, stepping through FRP tanks, electrical panel sparks, and tank truck fires have been added to the program, further enhancing the content of the training.
In fiscal 2023, 1,183 persons participated in training at the facility, bringing the total number since the establishment of the center to 14,536.
We have also installed hazard simulation equipment at each of our production sites (ENEOS: 11 sites, JX Advanced Metals: 4 sites). Workers at these sites, including those from contractor companies, are required to undergo training using this hazard simulation equipment before engaging in onsite work. With these and other efforts, we are working to ensure safety across the entire Group.
Using AI to Ensure Safety While Walking
In fiscal 2022, ENEOS introduced an AI-driven system for analyzing walking motion as a way to improve movement safety. The system uses a special device to measure a person’s walking speed, stride length, center of gravity, and other elements to determine the level of safety in the walking motion. The system then uses the results to provide suggestions for exercises or other ways to improve safety while walking.
In fiscal 2023, we added one of these systems to enable analysis of more people.
Improving Human Skills
As human factors are a major cause of occupational accidents and injuries, we have focused for many years on training to arm employees with the knowledge and technical skills needed to implement procedures and rules without fail. In recent years, however, there is growing awareness in the manufacturing industry, referencing leading initiatives in the healthcare and airline industries, about the importance of stepping up initiatives to improve non-technical skills, including status confirmation of work environments and communication among workers, in addition to compliance with procedures and rules. Accordingly, we are incorporating knowledge and activities for the improvement of these non-technical skills.
Foundation for Safe and Stable Operations
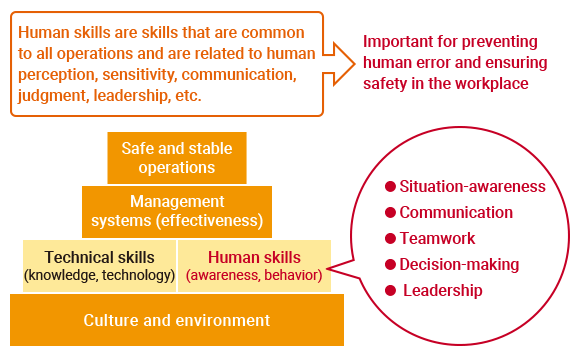
In the ENEOS manufacturing division, we refer to these non-technical skills as human skills, which we have stipulated in the activity guidelines for improving human skills in the manufacturing division. In accordance with these guidelines, at all of our plants and refineries, top management shares the importance of human skills, and systems have been put into place for the implementation of various forms of education and training and the integration of the resulting skills into existing daily safety activities in the workplace. In this manner, we are working to improve the human skills of all employees in the manufacturing division to prevent human-factor-related accidents and occupational injuries.
Initiatives with Contractor Companies
At ENEOS refineries and other facilities, we provide training for all contractor company employees that are new to our work sites on site safety rules and share information about onsite facilities. When selecting contractor companies, in addition to evaluating the safety management aspects of work execution, we conduct regular evaluations of the status of their safety management after the start of the business relationship, identify areas for improvement and follow up on the implementation status.
Moreover, in order to ensure proper safety management of contractor companies, we require the primary contractor to submit and execute a safety management plan, establish KPIs for the contractor company, conduct regular monitoring and evaluations, and report on improvements.
Main Initiatives at Refineries and Plants for Earthquakes
The ENEOS Group implements various earthquake measures at its refineries and plants.
Measures to Protect Lives
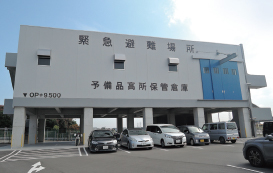
As a precaution against earthquakes and tsunamis, we have voluntarily implemented seismic reinforcement of our onsite offices and production unit control rooms, with priority given to the protection of human life.
We have also designated locations and methods for evacuation in case of an earthquake or tsunami, and we carry out disaster preparedness drills every year.
Measures for Seismic Reinforcement of Facilities
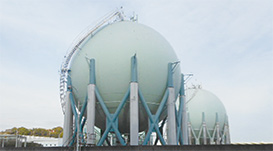
We are carrying out legally required seismic reinforcement work for tanks that store hazardous materials.
Upgrade work on floating-roof tanks subject to this requirement was completed before the statutory deadline. As for internal floating-roof tanks, which became subject to legislation in fiscal 2011, we completed seismic reinforcement work by the statutory deadline (end of fiscal 2023).
For high-pressure gas facilities, we have already completed seismic assessments following government instructions, as well as the retrofitting of spherical tanks with braces to increase earthquake resistance, taking into account the effects of the Great East Japan Earthquake. Seismic countermeasures for facilities of high importance were completed in fiscal 2021, marking the
completion of our seismic reinforcement of high-pressure gas facilities.
Measures to Mitigate Damage from Disasters
We have installed seismographs at all of our refineries and plants as part of a system that automatically shuts down equipment in a prompt and safe manner in the event of an earthquake, depending on the intensity.
Countermeasures against Accidents and Malfunctions
Disaster Prevention Facilities
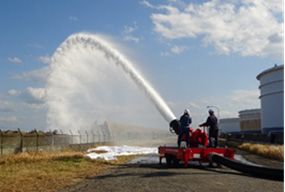
At our refineries, plants, and stockpiling terminals, we have established self-defensive organizations for disaster prevention and installed necessary disaster response equipment and facilities in preparation for potential accidents and disasters. We have also established a defensive organization for cooperative disaster prevention with nearby companies to improve the disaster preparedness of industrial complexes.
Oil Spill Countermeasures
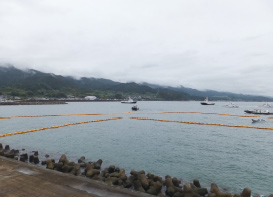
We have multiple oil dikes surrounding our storage tanks and systems to prevent leakage from spreading offsite. In addition, to promptly respond to oil spills at sea, we have oil fences to prevent oil spills from spreading and oil recovery vessels in place.
Fire Countermeasures
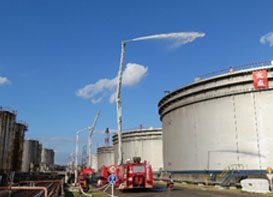
We have equipped our refineries and plants with fire extinguishing equipment, such as large chemical firefighting vehicles, high-altitude chemical water cannon vehicles, and high-capacity foam water cannon systems, for response in the event of a major fire.
Our facilities also have disaster response vessels with firefighting capabilities to respond to fires at sea.
Disaster Drills
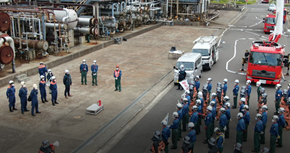
We regularly implement comprehensive disaster response drills for our self-defensive organizations for disaster prevention to ensure that we can respond in a quick and agile manner should an actual disaster occur. We also hold other drills, including joint disaster preparedness drills involving local fire departments as well as disaster response organizations from nearby companies and local communities.
Ensuring a Stable Supply
The ENEOS Group has established a backup system for ensuring a stable supply in the event of a major disaster that impacts the functions of production and shipping sites through collaboration with other production and shipping sites. We also conduct drills and training regularly to ensure that our sites can continue to function in the event of a disaster.