Basic Approach
At the ENEOS Group, we work to fulfill our social responsibilities across the entire supply chain by cooperating with suppliers of raw materials, logistics companies, construction companies, sales companies and others involved in our business activities, while carrying out initiatives for compliance, environmental preservation, human rights and labor, and health and safety.
In accordance with this approach, we have established basic principles on procurement in the Group Code of Conduct and the Group Procurement Policy, based on which we are implementing a number of initiatives. Based on the Group Code of Conduct and the Group Procurement Policy, Group companies have established their own procurement guidelines for business partners in accordance with their business characteristics, and carry out their procurement activities accordingly.
ENEOS Group Code of Conduct (excerpt)
- 3.Applicable Scope of the Code of Conduct
In principle, this Code of Conduct is applicable to all directors, officers and employees who work at ENEOS Holdings, Inc., and its subsidiaries. We also encourage companies that are part of our value chain to comply with this Code of Conduct. These companies include, but are not limited to, suppliers of raw materials, logistics companies, construction companies, and sales companies.
ENEOS Group Procurement Policy
All executives and employees of the ENEOS Group shall comply with this policy when they engage in procuring the goods and services necessary for business operations.
We also request that our suppliers understand this policy and guidelines and cooperate with us in following them.
- 1.Social Responsibility
The ENEOS Group will conduct procurement activities based on the ENEOS Group Code of Conduct, Human Rights Policy, and other policies in each sector. - 2.Selection of Business Partners
When selecting suppliers, the ENEOS Group will make fair and impartial judgments based on respect for human rights principles in Japan and overseas, and consideration for the environment, quality, and delivery times. - 3.Mutual Trust
The ENEOS Group emphasizes doing business with suppliers on an equal footing and aims to build mutually trusting relationships. - 4.Information Management
The ENEOS Group shall appropriately manage information obtained through its procurement activities.
Procurement Guidelines for Business Partners of Principal Operating Companies
Structure
For information about our structure, see ESG Management Structure.
Major Initiatives
CSR Procurement
The Group works with suppliers to promote procurement in which factors such as compliance, environmental impact reduction, human rights and labor, and health and safety are taken into account.
To ensure responsible procurement, employees in charge of procurement receive training to raise their awareness of the ENEOS Group Philosophy, the ENEOS Group Code of Conduct, procurement policies and applicable laws and regulations.
In contracts, which are the basis for purchasing transactions, and in the procurement guidelines for business partners established by each Group company, suppliers are asked to implement initiatives in 12 areas, including compliance, environment and human rights. The procurement guidelines also contain provisions for setting wages that at least meet minimum wage standards and payment of premium wages (overtime and holidays). All Group companies are required to comply with these guidelines.
In fiscal 2023, based on the results of human rights due diligence and the Corporate Human Rights Benchmark (CHRB) assessment, we continued to focus efforts on “consideration of human rights factors in supplier selection.” For details, see Human Rights Due Diligence.
Specific Actions to Support Living Wages for Suppliers
The procurement guidelines contain provisions for setting wages that at least meet minimum wage standards and payment of premium wages (overtime and holidays). All Group companies are required to comply with these guidelines.
CSR Procurement Workflow
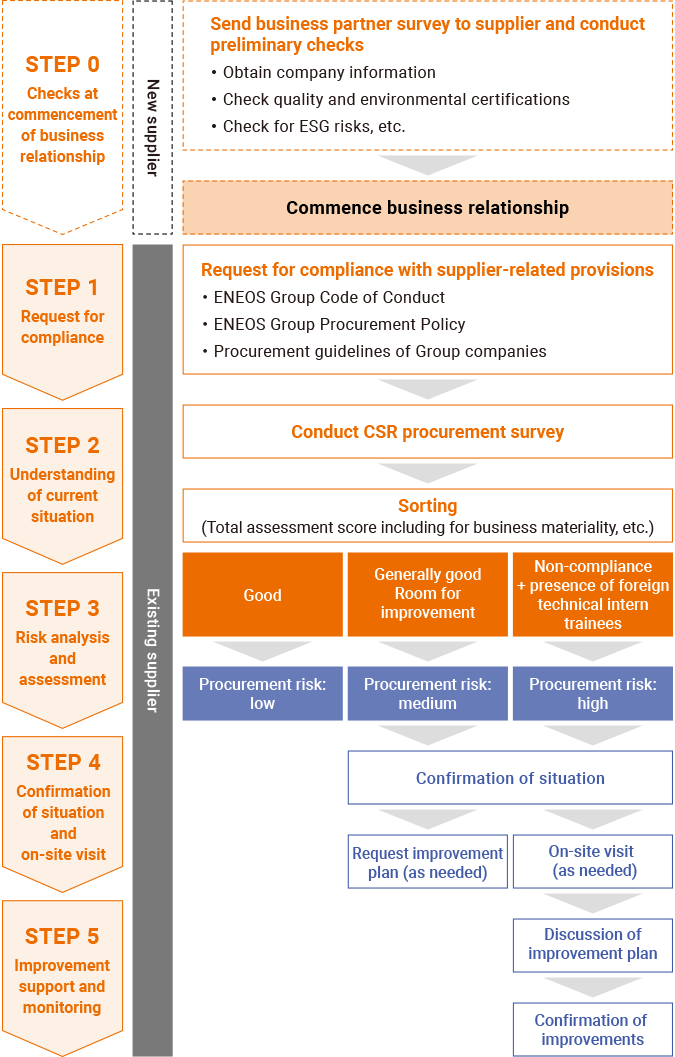
Checks at Commencement of Business Relationships with New Suppliers
When selecting a new supplier, the Group first confirms that the supplier has no relationship with anti-social forces. In addition to confirming the supplier’s financial position and performance, we conduct a comprehensive risk assessment by asking the supplier to complete our business partner survey, which includes items related to quality and environmental certifications, as well as ESG risks.
CSR Procurement Survey of Suppliers
The Group conducts CSR procurement surveys of its main suppliers to identify potential risks in the supply chain.
Through this survey, we assess risks related to environmental and social issues (human rights, labor, health and safety, etc.). For suppliers whose responses indicate the presence of risks, we conduct more detailed checks of those risks. In fiscal 2022, we revised the previous CSR procurement survey. In addition, before conducting CSR procurement surveys, we held briefing sessions for the suppliers to be surveyed. As a result, the response rate from ENEOS’s and JX Advanced Metals’ main suppliers exceeded 80%.
In fiscal 2023, based on the results of the survey, we conducted on-site surveys for the purpose of reducing supplier risks and communicating with suppliers, and in cases where improvements were necessary, we discussed improvement plans with the relevant suppliers and requested corrective measures.
CSR Procurement Survey Process
- 1.Selection of main suppliers
We select survey respondents based on our criteria for main suppliers. Main suppliers are selected based on the importance of the transactions in terms of sector*, transaction value, and substitutability, as well as factors such as past CSR procurement survey results, incident history, and ESG risks. In fiscal 2022, only domestic suppliers were subject to the survey.- *Suppliers with relatively high ESG risks from which we have ordered manufacturing materials, equipment, and construction that are of high importance to our business
- 2.Implementation of CSR procurement survey
We hold briefings on the importance of CSR procurement and our ESG initiatives with the selected suppliers, and then ask them to respond to the CSR procurement survey. Referencing the RBA1 VAP2 audit standards, the survey consists of 67 questions covering eight categories3: compliance and fair and equitable transactions, provision of products and services, information management, supply chain, environment, human rights and labor, health and safety, and dialogue and cooperation with local communities (see the table below). Items are classified into two categories: those related to the internal management structure, such as the clear documentation of policies and the identification of responsible parties, and those related to the status of activities, mainly those that can be quantified, such as the volumes of contaminated materials discharged and the number of occupational injuries.- 1Responsible Business Alliance. An industry coalition for ensuring responsible conduct in global supply chains within the electronics industry established in 2004. The RBA established the RBA Code of Conduct to ensure that working environments are safe, that workers are treated with respect and dignity, and that companies are environmentally conscious and responsible in their business activities. RBA member companies are required to abide by the RBA Code of Conduct. As of June 2024, the RBA has more than 230 member companies.
- 2The Validated Assessment Program (VAP) is an audit program in which a third-party auditor confirms compliance with the RBA Code of Conduct. VAP audits are conducted to ascertain whether compliance requirements are met in accordance with the VAP standards, which consist of labor, health and safety, environmental, ethics, and supply chain management.
- 3JX Advanced Metals’ CSR procurement survey consists of a total of 80 questions covering nine categories, including risk management.
- 3.Tabulation of survey responses and risk assessment
Survey responses are tabulated and scores are calculated for each question, enabling us to assess the management structure and status of activities of the supplier. - 4.Improvement support and monitoring
We ask suppliers for which risks have been identified to submit improvement plans. After that, we monitor the progress of their improvements.
CSR Procurement Survey Composition (Total of 67 Questions)
Category | Item (summary) | Number of survey items | Breakdown of individual items | |
---|---|---|---|---|
Compliance and fair and equitable transactions |
|
12 questions |
|
7 |
|
5 | |||
Provision of products and services | Appropriate provision of products and services | 5 questions |
|
3 |
|
2 | |||
Information management | Appropriate information management and information disclosure | 4 questions |
|
1 |
|
3 | |||
Supply chain | Supply chain management and supervision | 1 question |
|
1 |
|
- | |||
Environment |
|
17 questions |
|
6 |
|
11 | |||
Human rights and labor |
|
19 questions |
|
5 |
|
14 | |||
Health and safety | Ensuring safety and health enhancement | 8 questions |
|
3 |
|
5 | |||
Dialogue and cooperation with local communities | Dialogue and cooperation with local communities | 1 question |
|
- |
|
1 |
Risk Analysis and Assessment
Risk assessment involves the analysis and assessment of supplier responses to the CSR procurement survey according to four levels of criteria.
The following table contains a summary of assessment criteria and ENEOS’s response to the assessment findings.
Suppliers receiving the lowest assessment of “non-compliant” are identified as “high-risk suppliers” and are subject to intensive follow-up.
From fiscal 2022, suppliers who responded that they accept foreign technical intern trainees are also subject to follow-up interviews.
Risk Assessment Criteria and Response
Assessment | Explanation | ENEOS’s response |
---|---|---|
Good | Overall, sufficient measures are being implemented. | Each supplier receives a report on the survey results. Assessment results, including areas for improvement, are communicated to suppliers and information, such as the assumed risks for each category and information on relevant international guidelines, is provided. |
Generally good | Measures are being implemented for a relatively large number of items; risk is low. | |
Room for improvement | Measures are not being implemented for some items; risk is moderate. | |
Non-compliant | Items such as receiving adverse dispositions from government bodies, failing to confirm the facts and implement measures to prevent recurrence of violations, and the occurrence of serious occupational injuries are identified; risk is extremely high. | High-risk supplier. In addition to the response above, issue request for improvement and conduct monitoring, along with individual follow-up. |
CSR Procurement Survey Results
Since fiscal 2018, we have selected a total of 1,385 suppliers to complete the CSR procurement survey, with responses received from 1,306. Around 80% of suppliers who completed the survey were assessed as “good” or “generally good.” We also checked for child labor and forced labor, human rights risks of particular focus in the supply chain, but have not found any suppliers of concern in this regard.
CSR Procurement Survey Results (total of 1,306 suppliers)
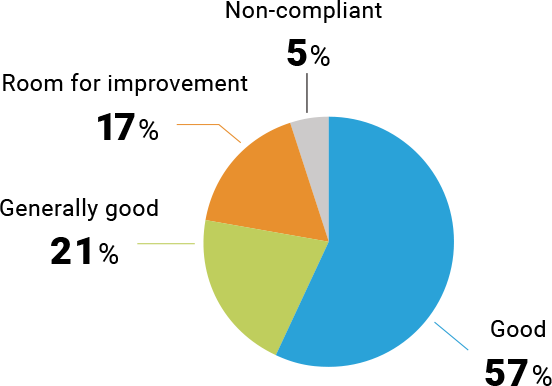
Improvement Support and Monitoring
Since fiscal 2023, we have been conducting on-site surveys with the aim of reducing supplier risks and expanding communication opportunities. We visit the sites of suppliers who are judged to have high procurement risks according to the results of the CSR procurement survey or are important for our business, where we conduct on-site inspections, check documents, and conduct interviews, to investigate the management system and the status of initiatives related to CSR procurement. The items to be checked were developed with reference to the RBA VAP audit standards.
As a result of the on-site surveys, we have classified items that need to be improved into “critical non-compliance” and “other non-compliance” and requested corrective measures from suppliers (see the table below). For suppliers who are judged to have “critical non-compliance,” we discuss the direction of corrective action, which leads to support for improvement.
In fiscal 2023, we visited three companies. We plan to continue conducting these on-site surveys, not only to confirm the status of responses, but also as opportunities to communicate directly with suppliers.
Classification of Non-Compliance and Deadlines for Corrective Action
Classification of non-compliance | Deadline for submission of corrective action | Approval of corrective action | Completion of corrective action | Applicable items (examples) |
---|---|---|---|---|
Critical non-compliance | Within 1 week of discovery | Within 10 days of discovery | Within 90 days | Violations of human and labor rights (forced labor, child labor, discrimination, etc.), inhumane treatment, serious occupational injuries, environmental damage that has a significant impact on communities, etc. |
Other non-compliance | Within 3 weeks of receipt of the survey report | Within 6 weeks of receipt of the survey report | Within 180 days of receipt of the survey report | Other insufficient initiatives in light of the Group’s Code of Conduct and procurement guidelines. |
Initiatives for Foreign Technical Intern Trainees
According to survey results, we conduct additional interviews with suppliers who responded that they employ foreign technical intern trainees to confirm that there are no issues with the legal compliance and employment status of the supervising organization and the host company.
Training and Awareness Activities
Supplier Briefings
The Group holds supplier briefings for suppliers subject to the CSR procurement survey with the aim of promoting understanding of the CSR procurement policy, the method for conducting the survey, and key points in conducting the survey.
In fiscal 2023, we invited approximately 200 companies to the briefings, where we shared the importance of CSR procurement, the Group’s ESG management, and the purpose and content of the CSR procurement survey to deepen their understanding of CSR procurement. In addition, with regard to human rights, which has become an increasingly important social issue, we explained the ENEOS Group Human Rights Policy, which is the Group’s basic approach to human rights, and our human rights initiatives, and requested suppliers’ understanding of and compliance with the policy.
Training for Employees Involved in Procurement
In order to promote responsible procurement throughout our supply chains, we believe it is important for the Group’s employees to understand CSR procurement. In fiscal 2022, in preparation for the on-site surveys to be conducted the following fiscal year, we held two study sessions for employees involved in procurement. In the first session, the participants learned about the CSR Procurement Guidelines, the content of the survey, and the content related to the implementation of the on-site surveys. In the second session, participants deepened their understanding of the procedures for conducting on-site surveys and the matters that should be confirmed during on-site surveys, referring to the RBA’s auditing standards.
Membership in Sedex and EcoVadis
In fiscal 2019, ENEOS became a member of both Sedex and EcoVadis, ratings providers for supply chain sustainability.
Confronting the Issue of Conflict Minerals
“Conflict minerals” is the general term for minerals that are mined (illegally, in most cases) in conflict-affected regions, providing a source of funds for local armed groups. The use of these minerals may lead to increasing human rights abuses and inhumane acts. In response to the international trend for stronger information disclosure and monitoring by stakeholders, industry organizations relevant to the JX Advanced Metals Group (including the LBMA1, LPPM2, and RBA) have established monitoring programs for eliminating conflict minerals, and require each business operator to undergo investigations and external audits.
- 1London Bullion Market Association. An industry association composed of financial institutions and others that deal in gold and silver ingot. Inclusion on this association’s Good Delivery List is viewed as a guarantee of high quality and reliability.
- 2London Platinum and Palladium Market. An industry association composed of financial institutions and others that deal in platinum and palladium ingot. Inclusion on this association’s Good Delivery List is viewed as a guarantee of high quality and reliability.
Initiatives for the Copper, Gold, Silver, Platinum and Palladium Supply Chains
JX Metals Smelting, a producer of gold, silver, platinum and palladium ingot, has established and operates a management system for supply chain due diligence that calls for confirmation of the origin of raw materials, risk assessments, and confirmation of distribution routes. The operational status is reported to the LBMA and the LPPM after undergoing an external audit by a third-party organization designated by these associations.
As a result of following these procedures, JX Metals Smelting’s gold, silver, platinum and palladium ingot are included on the Good Delivery Lists of the LBMA and the LPPM. Gold is also included on the RMAP Conformant Smelters list established by the RBA and GeSI1. This indicates that we are taking appropriate steps for the elimination of conflict minerals.
For copper ingot, we have established a management system for supply chain due diligence that calls for confirmation of the origin of raw materials, risk assessments, and confirmation of distribution routes. This system began operation in fiscal 2022. The status of its operation is monitored through external audits by a third-party organization through the procedures for obtaining the Copper Mark2 certification.
- 1Global e-Sustainability Initiative. A global trade association of information and communications businesses focused on achieving digital sustainability.
- 2A framework established in 2019 to demonstrate the responsible production of the copper industry and its contribution to the SDGs advocated by the United Nations. The Copper Mark certification is granted after independent third-party organization assessments covering compliance with environmental, human rights, community, governance, and other standards. Even after certification, performance is assessed every three years.
Initiatives for the Tantalum Supply Chain
As a smelter of tantalum, which is designated as a conflict mineral, TANIOBIS GmbH, a producer of tantalum powder in the JX Advanced Metals Group, conducts supply chain due diligence in accordance with international standards and strives to prevent complicity in human rights violations in conflict-affected and high-risk areas.
The company’s supply chain management has been certified by RMI1, an international framework for responsible mineral procurement, and it has been recognized as an RMAP2 Conformant Smelter.
- 1Responsible Minerals Initiative. Part of the Responsible Business Alliance (RBA), RMI promotes due diligence in the supply chains for conflict minerals and provides certification programs related to compliance.
- 2Responsible Minerals Assurance Process. A certification program for responsible sourcing of minerals established by RMI.
Initiatives with Distribution Companies
ENEOS shares its environmental and safety policies and targets for each fiscal year with the contract transport providers responsible for transporting its products in an effort to increase awareness of the environment and safety.
We also promote driving in an eco-friendly manner by holding the Ecodrive & Safety Workshop in partnership with vehicle manufacturers and encouraging participation in the Ecodrive Activity Concours hosted by an external organization. In addition, we are actively engaged in safety awareness activities, such as holding a safe delivery contest to improve tank truck drivers’ driving techniques and unloading work, and sharing good practices of transport companies at meetings of safety managers. In fiscal 2024, meetings of safety managers will be held in each district with the aim of stimulating case study sharing.
JX Advanced Metals continues to work on an appropriate response to the review of contracts with logistics companies, such as separating driving from non-driving ancillary work and considering and introducing fuel surcharges, to confirm its compliance with labor-related laws and regulations and laws and regulations related to the motor truck transportation business.
Through our initiatives to achieve sustainable logistics and distribution, we seek to increase the productivity of the entire supply chain, thus contributing to the fulfillment of our responsibility to provide a stable supply of energy and materials.
Support for the White Logistics Movement
ENEOS has supported the White Logistics movement since 2019 and JX Advanced Metals has supported the movement since 2020. This movement seeks to improve the productivity of truck transport, increase the efficiency of logistics and distribution, and ensure comfortable work environments for women and seniors. Both companies have submitted voluntary action declarations under this movement.
In addition, based on the revision of various laws and regulations aimed at reforming workstyles and improving logistics efficiency, we are responding to the associated “2024 logistics issues.”
In March 2018, ENEOS revised transport fees to improve the treatment of drivers and started early efforts to shorten working hours. The company revised transport fees in April 2024 and promptly responded to the recent wage increase momentum.
JX Advanced Metals investigated the waiting and handling times for cargo and is working to reduce them. The company is also taking measures to avoid placing an excessive burden on drivers, such as speeding up transportation requests to secure lead times for logistics companies.
ENEOS’s Voluntary Action Declaration and Initiatives
- 1.Proposals and cooperation for improving logistics and distribution
- 2.Separation of trunk route transport and collection/delivery transport
- 3.Encouraging use of expressways
- 4.Deliveries that avoid peak rush hour
- 5.Continuation of fuel surcharges
- 6.Suspending or stopping transport operations during extreme weather
JX Advanced Metals’ Voluntary Action Declaration and Initiatives
- 1.Proposals and cooperation for improving logistics and distribution
- 2.Separation of driving from other tasks
- 3.Consideration of modal shift for CO2 reduction
- 4.Agreements on fuel surcharges
- 5.Consideration of legal compliance in selection of contract counterparties
- 6.Safety measures during loading and unloading
- 7.Suspending or stopping transport operations during extreme weather